Ion beam sputter deposition
Adding a thin film
In ion beam sputter deposition the goal is to add a thin film to the substrate surface to change its material properties. The concept of ion beam deposition is an ion beam that sputters a target in proximity to the substrate. Ion beam deposition is a physical vapor deposition (PVD) technique. Other PVD methods are for example thermal or e-beam evaporation, magnetron sputtering, and pulsed laser deposition. Each technique has its advantages. For ion beam deposition these are predominantly the flexibility and precision in the deposition parameters, low sample impact, and high quality of the deposits.
Particle energies in ion beam sputter deposition
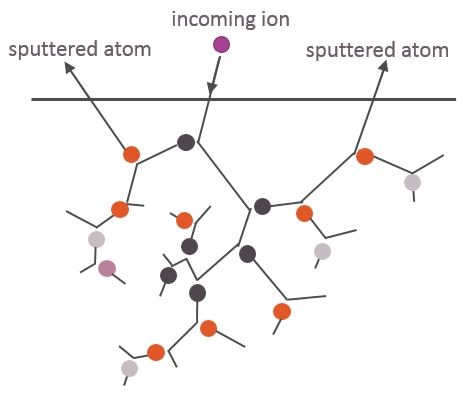
Ion beam sputter deposition compared to other PVD methods
The workhorse of industry in terms of PVD methods is magnetron sputtering. In magnetron sputtering an inert gas is ionized in a plasma between the substrate and the target, which is confined by a magnetic field. The target is biased and gets sputtered by the positive ions that are accelerated towards it.
A big difference between ion beam sputter deposition and magnetron sputtering is that for ion beam deposition there is no plasma between the substrate and the target. This means for ion beam deposition that also sensitive substrates can be deposited on, and the sputter gas inclusion in the deposit is likely to be lower. Also, in conventional ion beam deposition there is no bias between the substrate and the target, meaning both conducting as well as non-conducting targets and substrates can be used.
Furthermore, contrary to other sputtering methods, ion beam sputtering offers the ability to control independently and over a wide range the ion energy, flux, species, and angle of incidence.
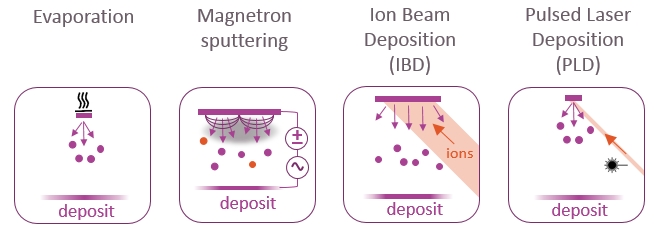
Pulsed laser deposition uses a laser directed at the target to vaporize the target material.
IBSD & Polygon Physics
Ion beam sputter deposition is probably the surface engineering process that Polygon Physics is most involved in. The traditional disadvantages of ion beam sputter deposition are high maintenance, high level of complexity, and difficulty to scale up. We are proud that because of our unique ECR technology these drawbacks are now part of the past.
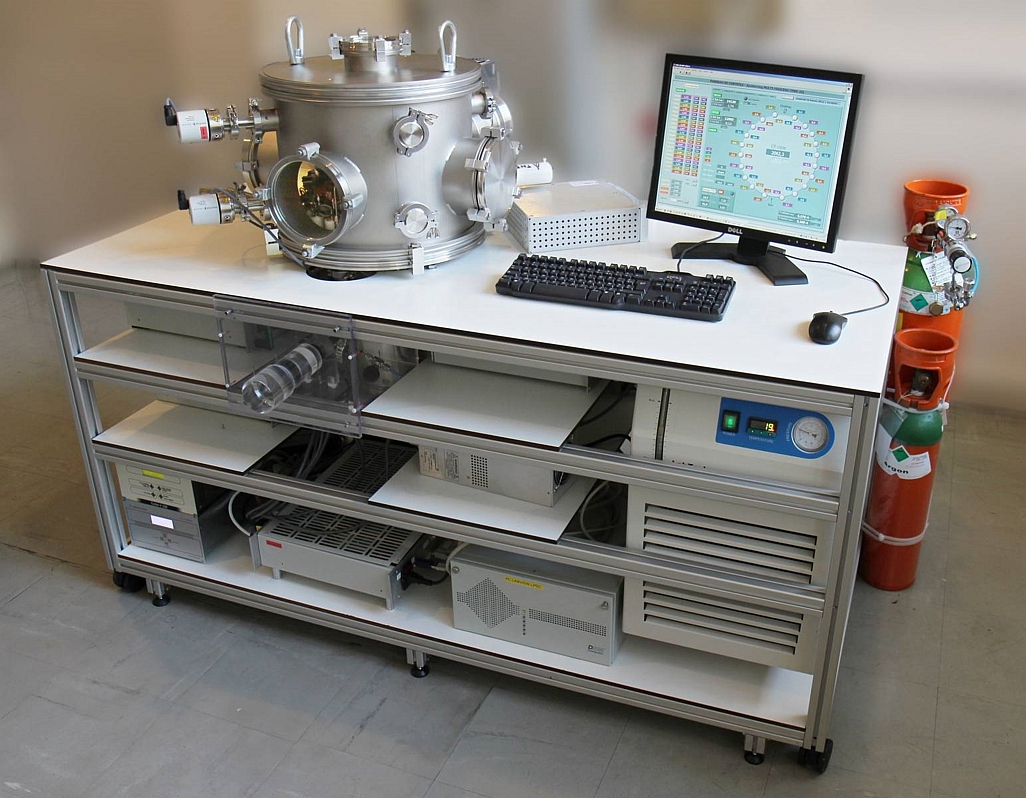